
Sinter Teknolojisi, metal tozlarının özel tasarım hassas kalıplarda preslenerek şekillendirilmesi ve atmosfer kontrollü fırınlarda sinterlenmesi ile çeşitli formlardaki parçaların üretilmesi işlemidir.
Üretim sürecindeki ana işlemler aşağıdaki gibi özetlenebilir:
-
Kalıp Tasarımı ve İmalatı
-
Toz Karışımının Hazırlanması
-
Sinter Presinde Tozun Preslenmesi
-
Sinter Fırınında Parçaların Sinterlenmesi
-
Çapak Alma
-
İkinci Presleme / Kalibrasyon (opsiyonel)
-
İkinci Sinterleme (opsiyonel)
-
Kaplama (opsiyonel)
-
Isıl İşlem (opsiyonel)
-
Yağ / Reçine Emdirme (opsiyonel)
Sinter kalıbı, talep edilen farklı parça formları için Sinter Teknik tarafından özel olarak tasarlanır. Kalıplar yüksek hassasiyetteki parçaların kalıptan rahat çıkabilmesine elverişli olacak şekilde dizayn edilir. Müşterilerimizin talebi üzerine hazırlanan kalıplar her müşteri için özeldir.
Talep edilen parçanın istenen yoğunluk, mukavemet, kırılma basıncı, sertliği gibi ölçütler göz önünde bulundurularak müşterilerin ihtiyacına yönelik doğru toz karışımı belirlenir.
Toz karışımının yanı sıra, preste farklı sıkıştırma oranları kullanılarak, farklı nitelikte parçalar elde etmek mümkündür. Düşük sıkıştırma oranıyla, düşük yoğunluklu, yüksek sıkıştırma oranıyla yüksek yoğunluklu parçalar elde edilir. Düşük yoğunluklarda, kendinden yağlamalı yataklar, gözenekli filtre elemanları elde edilebileceği gibi, yüksek yoğunluklarda, dişli, kama, kavrama gibi mukavemet isteyen parçalar elde edilebilir.
Presten çıkan parçalar, özel sinter fırını atmosferinde, farklı fazlarda sıcaklıklardan geçerek sinterlenir ve sert bir hale getirilir. Fırınlanan parçalardan daha yüksek sertlik talep ediliyorsa, parçalara ısıl işlem uygulanarak daha sert, aşınma direnci daha yüksek parçalar elde edilebilir.
Toz metalurjisinden üretilen parçalar, çeşitli endüstrilerde yaygın olarak kullanılmaktadır. En yaygın kullanım alanları şunlardır:
-
Otomotiv endüstrisi: Toz metalurjisi, otomotiv parçalarının üretiminde yaygın olarak kullanılmaktadır. Bu parçalar arasında, bronz burçlar, sinter bronz yataklar, demir burçlar, yağ pompa dişlileri, motor parçaları, dişliler, şanzıman parçaları, fren balataları, süspansiyon parçaları ve egzoz sistemleri yer almaktadır. Toz metalurjisinden üretilen otomotiv parçaları, geleneksel üretim yöntemleriyle üretilen parçalara göre daha dayanıklı ve hafiftir.
-
Tıbbi cihazlar endüstrisi: Toz metalurjisi, tıbbi cihazların üretiminde de yaygın olarak kullanılmaktadır. Bu cihazlar arasında protezler, implantlar, cerrahi aletler ve diş dolgusu malzemeleri yer almaktadır. Toz metalurjisinden üretilen tıbbi cihazlar, geleneksel üretim yöntemleriyle üretilen cihazlara göre daha uyumlu ve dayanıklı olabilir.
-
Havacılık endüstrisi: Toz metalurjisi, havacılık parçalarının üretiminde de yaygın olarak kullanılmaktadır. Bu parçalar arasında uçak motor parçaları, gövde parçaları ve şanzıman parçaları yer almaktadır. Toz metalurjisinden üretilen havacılık parçaları, geleneksel üretim yöntemleriyle üretilen parçalara göre daha hafif ve dayanıklı olabilir.
-
Enerji endüstrisi: Toz metalurjisi, enerji endüstrisinde de yaygın olarak kullanılmaktadır. Bu parçalar arasında nükleer güç santralleri için yakıt elemanları, rüzgar türbinleri için rotor parçaları ve güneş panelleri için çerçeveler yer almaktadır. Toz metalurjisinden üretilen enerji parçaları, geleneksel üretim yöntemleriyle üretilen parçalara göre daha dayanıklı ve verimli olabilir.
Toz metalurjisi, çeşitli avantajlara sahip bir üretim yöntemidir. Bu avantajlar, toz metalurjisinden üretilen parçaların çeşitli endüstrilerde yaygın olarak kullanılmasını sağlamaktadır. Bu avantajlar şunlardır:
-
Karmaşık geometrilere sahip parçaların üretimi için uygundur.
-
Geleneksel üretim yöntemlerine göre daha hızlı ve daha az maliyetlidir.
-
Daha az atık üretir.
Toz metalurjisi, gelecekte daha da yaygınlaşacak bir üretim yöntemidir. Bu teknolojinin avantajları, geleneksel üretim yöntemlerine göre daha rekabetçi olmasını sağlamaktadır.


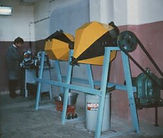
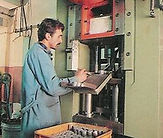

