
Self-lubricating bearings produced with sintering ensures:
High Precision,
Low Noise,
No-Maintenance,
Self Lubrication,
Potential to be used in many applications.
These are the parts that save you money.
Self-lubricating bearings are produced with sintering via compaction of metal powders. Metal powder mixture is compressed axially in a sintering mold. Compacted “cake phase” parts are heated in sintering oven atmosphere to a temperature below the melting point of the material. Diffusion creates bonds between metal powder particles. In the last stage, oil impregnation process is carried out by vacuum impregnation.
The most important point in self-lubricating bearings is the dimensional design, sintering material and used lubricant. All these metrics vary according to where the bearing will be used.
Especially sintered bronze is used in various applications, thanks to its high corrosion resistance and great working performance. For the parts which requires less resistance to corrosion, sintered iron can be a cost effective alternative to bronze.
Self-lubricating bearings can be cylindrical, flanged or circular. It can be designed in different shapes and tolerances on special request.
Bearings can be impregnated various oils, either synthetic or mineral for cost effectiveness, which sustains working performance between -65 Celcius to 200 Celcius degrees.
Comparison of Bearing Surfaces: Roughness of Working Surfaces
In self-lubricating bearings, hole surface plays a critical role in operation. Traditional methods for measuring surface roughness cannot give an accurate measurement in sintered parts. Traditional methods can mislead and results may appear as a rougher surface finnish quality due to porous structure of sintered parts.
Instead of traditional methods, “Abbot Curve” can be used to define surface roughness of sintered parts. Still, it would not be possible to get a 100% accurate answer. So, the best way is to align between customer and supplier on the desired quality and test and evaluate the results together.
Hydrodinamic Lubrication of Sinter Parts:
When there are two surfaces that are moving in contact with each other, surface friction occurs. If there is also a liquid phase material between these surfaces, and this liquid is also moving in the direction of suface motion, it results in hydrodynamic pressure which helps lubrication. Resistance against this pressure is dependent on the liquid viscosity. These are the main conditions of hydrodynamic lubrication. When the RPM is the low or radial lod is too high, lubrication may not be enough to separate both surfaces from each other, this situation may result in mixed friction.
Main Factors for obtaining a good efficiency from self-lubricating bearings:
The sinter bearing itself, oil, shaft which is in contact. The system can work well only when these three combined properly. Oil plays an essential role in this equation. The specific function of the sintered bearing depends also on the porosity amount which is obtained via sintering technology methods.
Amount of porosity can be increased up to 30% of bearing's total volume. Porosity volume is used for oil impregnation. Most pores are inter-connected and form a capillary like system and go up to part surface, thus providing whole of the part become impregnated. When the motion between the bearing and the shaft stops, there is very little oil left between two surfaces and oil amount increases when the motion starts.
When the shaft starts to move, a hydrodynamic film pressure occurs in the direction of the radial load, and a negative pressure is obtained on the side on which there is no radial pressure. As a result, oil moves towards the direction in which there is no radial pressure and maintains a continuous lubrication process between surfaces.
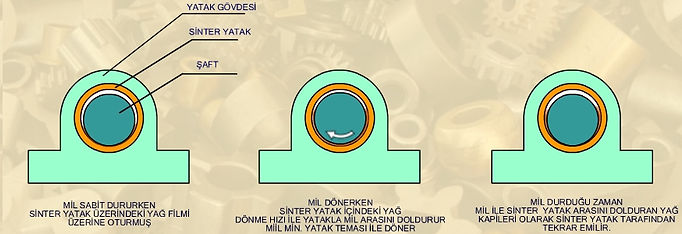
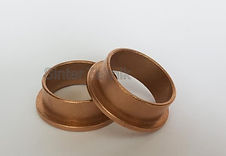