
Toz metal teknolojisi kullanılarak üretilen kendinden yağlamalı sinter burç ve sinter yataklar;
Yüksek hassasiyette,
Düşük sesle çalışan,
Bakım gerektirmeyen,
Kendiliğinden yağlamalı,
Birçok işlemde kullanılabilen,
Malzeme kullanımı ve üretiminde tasarruf sağlayan parçalardır.
Sinter teknolojisiyle üretilen kendinden yağlamalı sinter burçlar özel metal tozlarından üretilmektedir. Metallerin tozları bir kalıba boşaltılır ve eksenel olarak sıkıştırılır. Sıkıştırılmış haldeki “kek halindeki parçalar” korumalı sinter fırını atmosferinde, metalin erime noktasının altında kalan bir sıcaklığa kadar ısıtılır. Difüzyon sayesinde metal tozu parçalarının arasında bağlar oluşur. Son aşamada ise vakum emdirme yöntemiyle parçaya uygun olan yağ emdirme işlemi yapılır.
Kendinden yağlamalı parçaların en önemli noktaları tasarımı, malzemesi ve kullanılan yağlama maddesidir. Bunlar parçanın kullanılacağı yere göre değişmektedir.
Özellikle sinterlenmiş bronz, yüksek korozyon dayanıklılığı ve muhteşem calışma performanslarıyla birçok alanda kullanılmaktadır. Korozyon dayanıklılığının daha az gerektiği parçalarda, diğer teknik parametreleri sağlıyorsa sinterlenmiş demir kullanmak daha ucuz bir alternafit olarak tercih edilebilir.
Kendinden yağlamalı sinter burçlar, silindirik, flanşlı ya da dairesel olabilir. Özel talep üzerine değişik şekillerde ve toleranslarda çalışılabilir.
Uygulamaya göre yataklara -65C ile 200C arasında sorunsuz çalışmalarını sağlayan, değişen viskositelerde sentetik ya da daha uygun maliyetli olan mineral yağlardan emdirilebilir.
Yatak Yüzeylerinin Karşılaştırılması: Çalışma Yüzeylerinin Pürüzlülüğü
Kendinden yağlamalı sinter yataklarda, deliğin yüzey karakteristiği, çalışma özellikleri açısından önemlidir. Katı malzemelerin yüzey pürüzlülüğünü ölçmek için kullanılan standart testler gözenekli yapısından ötürü yanlış sonuç vereceğinden sinter parçalarda kullanılamaz, kullanıldığı taktirde yüzey normalden çok daha pürüzlüymüş gibi bir sonuç elde edilecektir.
Toz metal teknolojisiyle üretilen parçaların yüzey pürüz miktarını belirlemek için “Abbot Eğrisi” kullanılabilir. Yine de garantili bir sonuç elde etmek bu yöntemle de tam olarak gerçekleşememektedir. Bu yüzden müşteri ile üretici, kendi yöntemlerini belirleyip gereken özelliklere göre bir karşılaştırma ve değerlendirme yapmalıdır.
Sinter Parçaların Hidrodinamik Yağlanması
Birbirine bağlı olarak hareket eden iki parçanın yüzeyi temas ediyorsa yüzeyde sürtünme oluşur. Yüzeyler arasında sıvıdan bir film var ise ve bu yağ hareketin yönüne yakınsıyor ise hidrodinamik basınca sebep olur. Harekete gösterilen bu direnç ise yağlamanın viskositesine bağlı olarak değişir. Bunlar hidrodinamik yağlamanın koşullarıdır. Yetersiz dönme hızında ya da aşırı yük durumunda, aradaki yağlama miktarı iki yüzeyi birbirinden ayırmaya yetecek kadar kalın olmaz. Bu gibi durumlar karışık sürtünmeye sebep olur.
Kendinden yağlamalı sinter yatakların iyi çalışabilmesi üç temel faktöre bağlıdır:
Sinter yatağın kendisi, yağ ve yatağın temas ettiği şaft. Ancak üçünün beraberliği efektif bir biçimde oluyorsa, sistem doğru bir biçimde çalışabilir. Bu ilişkide yağ önemli bir rol oynamaktadır. Sinter yatağın özel işlevi gözenek miktarına bağlıdır ve bu miktar sinter teknikleriyle elde edilir. Gözenek miktarı, yatağın tüm hacminin %30’una kadar çıkarılabilir. Bu gözenek hacmi, yağ emdirmek için kullanılır.Çoğu gözenek birbirine bağlıdır ve kılcal damarlar gibi bir sistem oluşturur ve yüzeye kadar gider, böylelikle parçanın birçok yerine yağ akışı sağlanır. Parçalar hareket etmediğinde bu kılcallardaki kuvvetlere bağlı olarak yatak ile şaft arasında çok az yağ bulunur. Şaft hareket etmeye başladığında, yük çizgisi yönünde hidrodinamik film basıncı oluşur, yüklemenin olmadığı taraftaysa negatif bir basınç oluşur. Bunun sonucunda yağ, yatağın gözenek duvarına doğru sirküle eder, yük çizgisinden uzaklaşarak yükün olmadığı tarafa doğru ilerler. Statik stres ya da dinamik dengesizlik sebebiyle yük basıncı artar ise karışık sürtünmeye sebep olur. Şaft durduğunda yağ tekrar kılcal gözeneklerdeki kuvvet ile geri emilir ve döngü durur.
Katı Kayganlaştırıcıların Eklenmesi
Katı kayganlaştırıcılar, normal yağ kayganlaştırıcıların yetersiz olduğu durumlarda kullanılır, örneğin sıcaklığın 300 C’ye ulaştığı ortamlarda ya da sık sık kenar yağlama operasyonlarında kullanılan parçalar için gerekebilir.
Demir ya da bronz yataklarda malzemeye grafit tozu eklenmesinin en iyi toz kayganlaştırıcı olduğu kanıtlanmıştır.
Özel bir kayganlaştırıcı olarak, Molibdenum Disulfide (MoS2) kullanılabilir. Bu toz kayganlaştırıcı özellikle, yağ kayganlaştırıcıların yıkanarak yataktan çıkabileceği durumlarda kullanılır. Örnek olarak deniz pompalarında kullanılan sinter yatakların matriksinde MoS2bulundurularak gresleme garanti edilir.
Yatak ölçülerinin, malzemesinin ve greslemenin düzgün seçimiyle, kendinden yağlamalı sinter yatakların ömrü, dahil olduğu assemblenin türüne ve etrafındakı koşullara (dönme hızı, sıcaklık, yük, çalışma boşluğu ve yağın korunumu) bağlıdır.
Yatak Ömrü İçin Genel Kurallar:
1) Hiçbir özel koruma olmadan ve yağ kaybı olmaksızın normal çalışma koşullarındaki yatak sistemleri: 2000 saate kadar.
2) Ekstra gresleme yapılmış ancak yağ resirkülasyonu olmayan, normal çalışma koşullarındaki yatak sistemleri: 5000 saate kadar.
3) Ekstra gresleme yapılmış ve garantili yağ resirkülasyonu olan, normal çalışma koşullarındaki yatak sistemleri: 5000 saatin üzerinde.
Kendinden yağlamalı sinter yataklarda kullanılan özel yağlamalar; sıvı, toz ya da macunsu olabilir. Sıvılar parçaya emdirilerek ya da ekstra yağlama yaparak, macunlar ekstra yağlama yaparak, tozlar ise sinter yatağın toz karışımına eklenilerek kullanılabilir. Devam eden bölümde yaygın olarak kullanılan sıvı kayganlaştırıcılar ele alınacak ve sentetik ile mineral yağlar olarak gruplandırılacaktır.
Mineral (Madeni) Yağlar: Ekonomik fiyatları ve iyi yağlama özelliklerinden ötürü mineral yağlar en çok kullanılan kayganlaştırıcı yağlardandır. Ana malzemeleri rafine edilmiş naphtenic ya da paraffinic yağ ürünleridir, bu sebeple içeriklerinde doğal çeşitlilikler olabilmektedir. Hemen hemen tüm mineral yağlar, gerekli özelliklere sahip olabilmeleri için ek maddeler içermektedirler. Yalnızca -35C ile +90C arasında kullanılmaya elverişlilerdir.
Sentetik Yağlar: Birçok çeşit saf sentetik yağ bulunmaktadır. Aşağıdakiler sinter yataklamada parçaya emdirilmek için kullanılan sentetik yağlardır: Ester, Sentetik Hidrokarbon, Poliglikol, Silikon (Florin katılarak da kullanılabilir), Perflorinlenmiş polyester.
Sentetik yağın avantajları yüksek oranlardaki saflığı ve mineral yağlarla karşılaştırdığında çok daha üniform yapıya sahip olmasıdır.
Sentetik Yağ Çeşitleri:
1) Ester Yağlar: Di-ester yağlar sinter yataklarda özellikle çok iyi ıslanma kaliteleri sebebiyle kullanılır (yüksek derece polarize parçalardan oluşurlar). Bu yağlar -65C kadar düşük derecelere dayanır ancak çok yüksek sıcaklıklarda madeni yağların performansını geçemezler. Diğer sentetiklerle karşılaştırıldığında korozyona uğrama ihtimallerinin daha yüksek oluşu ve 90C’nin üzerindeki ortamlarda bakır yoğunluklu parçalarla katalitik reaksiyona girebilme ihtimalleri, ester yağların dezavantajıdır.
2) Sentetik Hidrokarbon: Temel kimyasal yapıları madeni yağlarınkine benzer. Düzenli molekül yapısı sayesinde iyi viskosite/sıcaklık davranışı ve yük-kapasitesi uygun bir fiyata elde edilir.
3) Poliglikol: Bu yağların pozitif özelliği, karışık sürtünmenin olduğu durumlarda bile harika yağlama ve yük kapasite özelliklerinin korumalarıdır. Bu yağlar yüksek sıcaklığa da direnç gösterirler. Dezavantajı ise bazı poliglikol çeşitlerinin higroskopiye(su emme yeteneği) yatkın olmasıdır. Bu da bronze sinter yataklarda bile korozyona sebep olabilir. Poliglikol yağlar madeni yağlarla karıştırılamaz.
4) Silikon Yağlar: Neredeyse ideal viskosite özelliklerine sahiptirler, viskositeleri sıcaklıktan etkilenmez bu sayede 150C yüksekliğe kadar kullanılabilirler (hatta fluorosilikonlar 180C’ye kadar). Ancak silikon yağlar iyi bir kayganlaştırıcı değildir, akmaya (sürünmeye) meğillidirler, bu da yük kapasitesinin düşmesine neden olur. Flor katılmasıyla silikon yağlar iyileştirilebilir ancak bu da masraflı bir yöntemdir.
5) Perflor Polyester Yağlar: Bu yağ grubu termal stabiliteleri ve oksidasyona dirençleri sayesinde 200C sıcaklığa kadar en iyi performansı göstermektedir. Ancak korozyon dirençleri düşüktür ve yüksek fiyatları sebebiyle yalnızca özel uygulamalrda kullanılmaktadır.
Yağların Özellikleri:
1) Mekanik Kapasite: Mekanik kapasite yağın yük kapasitesini, dolayısıyla da performansını etkileyen temel faktörlerdendir. Yağın kapasitesi ne kadar fazlaysa, aşınma da o kadar azdır. Tabi ki bu ancak şaftın, yatağın ve montajın tasarımı doğru yapıldıysa gerçekleşir. Genel olarak denilebilir ki, yük ne kadar az ise viskosite de az olabilir. Ağır yüklerde viskositeyi de arttırmak gerekir. Buna karşın, çalışma performansı, çalışma hızı ve sistemi soğuk başlatabilme yeteneği de göz önünde bulundurulmalıdır.
2) Viskosite: Viskosite birbirine karşı hareket eden sıvı moleküllerin iç sürtünmesidir. Akışmazlık olarak da düşünülebilir. Düşük viskositeli sıvılarda, yüksek viskositelilere göre daha az sürtünme vardır. Bir yağ çeşidi seçilirken, yatağın çalışacağı sıcaklık göz önünde bulundurulmalıdır, çünkü viskosite sıcaklığa göre değişir. Yüksek viskosite daha iyi mekanik kapasite demektir, ancak aynı zamanda daha fazla dinamik sürtünme ve sıcaklık anlamına da gelir. Genel prensip olarak, viskosite soğuk başlangıç problemlerini önleyecek kadar düşük olmalı, ancak yüksek sıcaklıklarda yük kapasitesini koruyabilecek kadar da yüksek olmalıdır.
3) Termal Kapasite: Yatakların düzgün çalışabilmesi için, viskositeyle sıcaklığın ilişkisi göz önünde bulundurulmalıdır;
-Düşük sıcaklıklarda (-50C’den -20C’ye kadar) sentetik yağlar, madeni yağlardan daha uygundur. Genelde viskositesi 40C’de 15’den 70 mm²/s ‘den az olan yağlar kullanılır. Uygulamanın üst sıcaklık limitine göre tercih yapılmalıdır. Tercih edilen yağlar, ester, hidrokarbon ve silikon yağlardır.
-Normal Sıcaklıklarda (-20C’den +90C’ye) , 40C’de 68mm²/s viskositesi olan rafine edilmiş parafinli madeni yağlar tercih edilir.
-Yüksek sıcaklıklarda (90C’den +200C’ye), yalnızca, 40C’de 100 ile 400 mm²/s arasında viskositesi olan sentetik yağlar tercih edilebilir.
4) Yıpranma/Oksitlenme Stabilitesi: Yağın yıpranmaya ve oksitlenmeye karşı stabilitesini koruyabilmesi, korozif maddelerin, yükün, sıcaklığın ve suyun sebep olabileceği kimyasal bozulmalara karşı gösterdiği direnç anlamına gelir. Uzun zaman boyunca gösterilen stabilite, kendinden yağlamalı sinter takımının da uzun süreler boyunca çalışmasında önemlidir.
5) Buharlaşma Eğilimi: Yatağın çalışma sıcaklığı ne kadar yüksek ise, yağın buharlaşarak bir miktarını kaybetme ihtimali de o kadar artar. Buharlaşma ihtimali ne kadar az ise yağlama stabilitesini o kadar uzun süre korur.
6) Sentetik Malzemelerle Uyumluluğu: Sentetik rulmanlar ya da yatak pulları kullanıldığında, yağın bu malzemelerle uyumluluğu kontrol edilmelidir. Silikon yağların dışındaki yağlarda, sentetiğin yapısına az da olsa zarar verme eğilimi vardır. En agresif yapıdaki yağlar, ester yağlardır.
7) Yağların Karışabilirliği: Aynı tipteki yağların dışındaki yağlar karıştırılmak istendiğinde yağlama özellikleri değişebilir, önceden kontrol edilmelidir.
Destekleyici Yağlama:
Kendinden yağlamalalı yataklar zamanla merkezkaç kuvvetinden ve buharlaşmadan ötürü yağ kaybı yaşarlar. Kayıp miktarı %40’a ulaştığı zaman, sinter yatak kullanılamaz hale gelir. Merkezkaç kuvvetinden ötürü yaşanan kayıp, takıma eklenebilecek metal bir plaka ya da keçeyle engellenebilir. İç çapta genişletilmiş kanallar kullanmak da bir çözüm yöntemi olabilir. Ek bir yağlama rezervuarının yapılması parçanın ömrünü uzatabilir. Operasyonun etkililiği seçilen rezervuarın çeşidine göre değişir. Bunlar; yağ emdirilmiş keçe, plastik rezervuar, makine yağı, yağ emdirilmiş lifler olabilir. Bunların bir kombinasyonu da kullanılarak yatağın etrafındaki boşluklara yerleştirilebilir. Ek rezervuarla yatak arasında iyi bir kontak olursa sistem doğru bir biçimde çalışacaktır.
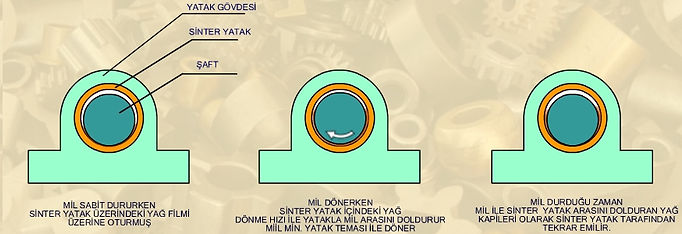
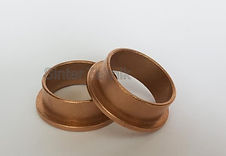